Maintenance Experience of Model 1515 Shuttle Loom
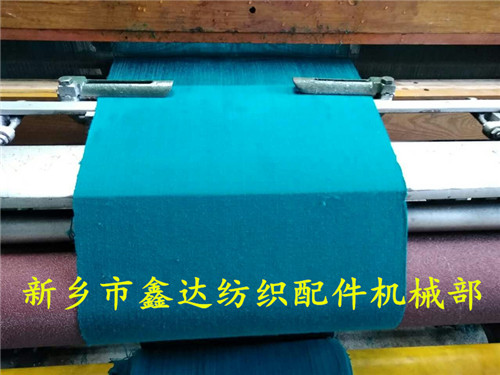
This paper introduces in detail the maintenance experience of 1515 shuttle loom (the causes of inferior products in the process of fabric weaving). It briefly discusses the weaving experience, analyses the maintenance of loom, and finds out the reasons for inferior products. It clearly lists the warp broken ends, Weaving experience, loom maintenance, defective reasons, fabric weaving,weft shrinkage, weft broken, thinning, weft tail weaving, jumping pattern, spider web, dense path, square eye, rough fabric surface and reed marks. Reasons for the formation of defective fabrics such as edge bracing, broken yarn, wool edge, towel edge, tight edge, bag shape, hard edge, loose warp, tight warp, tufted, edge cobweb, uneven fabric edge, narrow edge, flanging, velvet ball, bending weft, bow weft, broken hole, staggered weft, flying flower, wide width, etc.
1. Warp Breakage Reasons (excluding yarn quality and preparation reasons)
1. The heald frame is too high or low and uneven.
2. Opening too large or too small, too early or too late.
3. Warp yarn is too short, (back beam before), warp tension is too large.
4. The position deficit of rear beam and warp stop is high, and the tension gap between upper and lower warp is too large.
5. The distance between the stop frame and the heald frame is too far and too low.
6. Air conditioning and humidity are too high or too low. (In particular, hemp yarn has the greatest reaction)
7. Roughness of sword neck, reed, heddle, menopause piece, sword belt, etc.
8. Over-braced position is too high, should be 1 mm from the lowest position.
9. Knot yarn tail, flying flowers and sundries are stirred into warp yarn.
10. On duty, bad handling of warp upside-down and stirring ends and bad yarn knot after warp breakage, such as yarn tail length.
2. Reasons for weft breakage
1. Weft strength is too low, loose twist yarn, big knot, cottonseed scrap, flying back yarn clamping.
2. Too much strength, too much tension and bad forming when winding.
3. The edge braces the reed too far, and the distance between the reed and the reed is less than 1 mm.
Third, weft shrinkage
1. Weft twist is too large.
2. Weft is too dry or wet.
3. The opening is not clear.
4. Opening too early or too late.
5. Weft drawing tension is too small.
6. Warp tension is insufficient.
7. Weft bobbin has large knots, flying flowers, debris attachment and slub yarn, which causes part of the opening unclear.
4. Small and thin roads
1. Reed and burr roll loosen or corrode.
2. Warp tension is too large or too small.
3. The tension difference between upper and lower warp layers is great.
4. The shuttle opening was not corrected when driving after parking too long.
5. Starting too slowly after parking affects beating-up force. The belt of the main motor is loose and weak.
V. Weft End Weaving
1. The right warp yarn is too far away from the downwind pipe, and the waste side yarn can not hold the end of the yarn well.
2. The weft tension is too small and the blade opens too late.
6. Rare roads
1. The causes of weft breakage are weft breakage. First of all, weft breakage should be reduced.
2. The weft-breaking winding and unwinding device is not good.
7. Flower Jumping
1. The heald frame is loose, uneven or too low.
2. Warp tension differs greatly between upper and lower layers.
3. Sizing overhairing, opening stickiness and poor sizing result in down ball or hairiness.
4. Warp yarn has flying wool, tail and big end.
5. The end of the heddle is broken or the heddle is disturbed.
6. Looseness or low tension of some warp yarns.
7. The opening time is not right. (too small opening)
8. Side support is not standard.
9. Reed number is too dense. Please check reed number and process sheet.
10. Check the process sheet if there are too many reed roots per reed.
8. Cobweb
1. The density of the menstrual stop tablet is high, and it will not stop immediately after menstruation break.
2. Flowers accumulate between menopausal segments and cause motion failure.
3. There are flying flowers, yarn tails and sundries in the opening.
4. Heddle breakage.
5. The tension of the weft yarn is suddenly too large, and the side brace breaks the weft yarn into a side cobweb.
6. The menopausal tablet is incomplete, bent and too light (weight).
7. There are more than two warp yarns in a warp stop slice.
8. Other causes of menorrhagia.
9. Secret Road
1. When the Turner breaks the weft, he withdraws too much cloth or too much cloth when he breaks the cloth.
2. The coiling part is stuck with debris or not lubricated enough.
3. Burr rollers and burrs are severely damaged or worn.
4. Pressure of cloth roller is not enough or bending.
5. The coil is not tightened when the cloth is dropped.
6. The rollers are too smooth.
10. Reed marks, square eyes and rough cloth surface.
1. The tension difference between upper and lower warp yarns is too large.
2. The heald frame is uneven, too high or too low.
3. Warp tension is too big and too small.
4. The rear beam is too low and the stop frame is too low.
5. The opening is too big or unclear.
6. Opening too late or too early.
7. Sizing is too hard.
8. Too many warp roots per reed.
9. Sizing is too wool and opening is sticky.
10. Reed teeth are too thick or unevenly distributed.
11. The workshop is too dry.
12. The weft tension is not uniform.
XI. Edge bracing defects
1. Side support needle size is too thick or too thin.
2. Bending or breaking of edge supporting needle tip.
3. The spinning of the burr ring on the side is not flexible or worn out.
4. The position of side brace is not right.
5. Fabric tension is too high or too low (warp tension)
6. Weft tension is too high.
7. Flying flowers, sundries and yarn tails are clamped in the side braces.
XII. Broken Side Yarn
1. Flexible rotation of side brace or wear of burr roll.
2. The position of side brace is too high or too low.
3. The reed teeth are extruded, bent or loosened or rough.
4. The opening time is not appropriate.
5. Ribbon selvage, opening too large, too low, too high, too early or too late.
6. Warp reed width is too wide or too narrow.
7. The warp yarn of the spindle is too wide or too narrow.
8. Weft drawing tension is too high.
9. Side yarn wearing method and number of side yarns are not suitable.
10. Warp tension is too large or too small.
11. Side yarn sags when the spindle is winded.
13. Wool and towel edges
1. The weft drawing tension is too low.
2. Side yarn wearing law is not regulated.
3. Too high, too low, too early, too late or unclear opening.
3. Reed and reed teeth are loosened or extruded.
4. The position of side braces is too high, too low, and the queen mother.
14. Close-edged, Bag-shaped, Hard-edged
1. Excessive number of reed roots per side yarn can be improved after reducing.
2. Weft tension is too high.
3. Side yarn tension is too high.
4. Modification of plain yarn to 2/2 ribbed yarn can improve most of them.
5. Side yarn wearing errors.
6. The side braces are too short or not enough, and the stretching tension is insufficient.
7. The Queen Mother.
8. Width of weaving axle differs greatly from width of cloth.
15. loosening and tightening meridians
1. Warp yarn upside-down end (parallel axis)
2. More than two warp yarns are bonded and loosened when separated during weaving.
3. Winding of warp yarn and stop piece.
4. When warp flying yarn passes through bad line, it is tight and loose.
5. Bad filament.
6. When warp winding, the knot stretches relaxedly.
7. The waste warp yarn is wound around the weaving shaft to press the adjacent yarn.
8. There are flying balls on the warp yarn, and the tail of the yarn is wound around the heddle and the warp stop slice.
9. The warp yarn tension is higher when the spindle is winded too loosely and the warp yarn sags.
10. The sizing time of the spindle varies, and the loosening time varies.
11. The warp stop frame is too far from the heald frame (slow speed)
12. The menopausal tablet is too light and bent.
16. Clustering
1. A tuft of warp yarn is elongated after removal of tail-clip yarn or flying debris of broken ends of warp yarn.
2. The knots on the warp lengthen a bunch of warp yarns.
3. The warp yarn is elongated by reducing the external force.
Seventeen. Uneven Edge
1. Weft drawing tension is too small or too large and uneven.
2. The warp yarn of the spindle is too wide.
3. Side weaving opening is too large, too low or after side weaving heald frame.
4. There are flying yarn tail impurities in the shuttle eye.
18. Edge cobweb
1. There are yarn tails and flying flowers in the heddle.
2. The tension of weft yarn is too large and the tension of warp side yarn is especially small.
3. The position of side brace is queen.
4. Side yarn is not worn properly and twisted side yarn.
19. Narrow edges
1. The number of side yarns is too small.
2. Weft tension is too strong.
20. Unbounding
1. There are tail yarns in the opening of side yarn.
2. The opening time of side weaving is not suitable.
21. Cashmere ball
1. Sizing rate is too low.
2. inappropriate slurry matching
3. Too much wax.
4. Warp is damp or mildewed.
5. Warp drying is not enough.
6. Reed teeth are rusty or rough.
7. The menopause frame is skewed or the menopause tablet is overweight.
8. Warp tension is too strong
Twenty-two. Bending and bowing latitudes
1. The position of the side brace is too high or the queen mother.
2. The length of side brace is not enough.
3. Needle size is too thin.
4. Side yarn tension is too large or too small.
5. Side yarn is too dense for reed threading.
23. Oil Pollution
1. Stain on worsted yarn, winding yarn and sizing yarn in the former process.
2. Contamination in transportation.
3. Repairers and locomotives are not clean.
4. In other cases.
Twenty-four. Holes, Tears
1. Hard or sharp objects collide with cloth surface or coil burr roll.
2. Burr roll and edge breakage.
3. Friction in full roll and edge handling.
4. Needle size of side-supporting burr ring is too thick or too thin.
5. Cloth tension is too tight
26. Uneven dyeing
1. Mixing cotton with yarn is not uniform or mismatched.
2. There are great differences in yarn twist.
3. The conditions of yarn stabilization are not uniform.
4. Mildew or grease stain with yarn.
5. Sizing with excessive wax.
6. Sizing size is not easy to fade.
7. Some warp yarns suffer accidental rubbing.
Twenty-seven. Mismatched latitude
1. Weft insertion errors
2. Misuse of Pipe Color
3. Mismatched yarn in winding
4. Different Weft Yarns Used by Lathe Workers on Other Machines
Twenty-eight. Weaving of foreign fibers, flying flowers and miscellaneous fabrics
1. Stain on worsted yarn, winding yarn and sizing yarn in the front process.
2. The cheese yarn is not clean.
3. The cloth machine is not clean.
4. Poor cutting method.
5. Bad working method on duty.
29. Broad and narrow
1. Reed number is not suitable.
2. Error or inaccuracy of reed number.
3. The humidity in the workshop is too high or too low.
4. Warp tension is too small or too large.
5. Too many or too few copies.
6. Excessive or insufficient number of reeds per reed of side yarn
7. Use wrong fine or thick weft or too dense weft.
The original source of the article https://www.meipian.cn/nhq10sc