Weaving Process And Technology
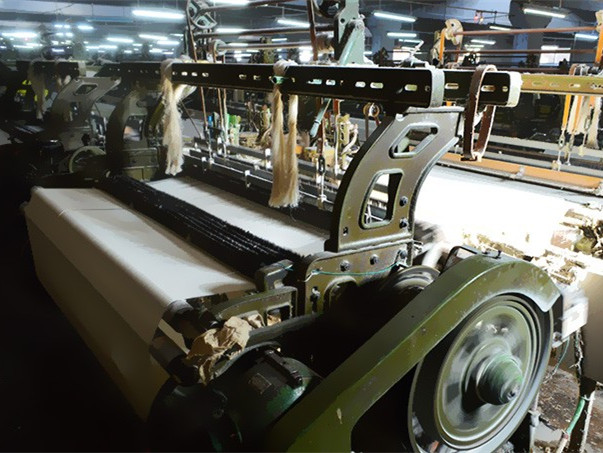
Section 1 shed,
No.1 the shape of the shed
The warp on the loom is arranged along the longitudinal (front and back) sides of the loom, as shown in figure 7-1. From the warp beam winding leads, after the E and stop frame guide rod D, through the eye C and reed, the cloth B with weft woven cloth, and then passes over the front A, then wound onto the cloth roll formed on the cloth roller.
With the opening, the warp of heald frame motion is divided into two layers, forming a prismatic channel BC1DC2, which is shed. Form a layer of warp yarn above the shed, BC1D is the upper warp, and the lower BC2D is the lower warp. When the shed is fully closed, the two - layer warp is returned to its original position with the heald frame, BCD. This position is called the heald position of the warp.
The size of the shed is usually measured by the height of the shed, the length of the shuttle and the angle of the shuttle. With the opening of warp heald frame when moving maximum displacement is called C1C2 height H shed from the mouth to the fabric, B guided D frame rod stop between horizontal distance to shed the length of it by the first half length L1 and after half length L2, ratio of L1 and L2 is called shed symmetry. The shed in front of the BC1C2 is part of the shed, the shuttle or other weft insertion device from here through and into the weft, warp and weft finish, called rake angle C1BC2 angle C1DC2 called the shed, shed angle. Usually, the same height in the shed, in order to get a relatively large height angle and reed mouth before the shuttle before the shed (upper and lower warp and reed intersection distance) for weft insertion, often used in front of the shed length is less than half the length of the mouth after the asymmetric spindle.
The warp in the heald level position, warp knitting to the connecting wire beam with relevant contact parts called warp position line, as shown in Figure 7-1 connection BCDE. If D and E are on the extension line of the BC line, the warp position line will be a straight line, called a straight line. A straight line is a special case of the warp line. Broken line ABCDE is called loom line. In general, the shape of the shed is asymmetrical in the direction of the height of the shuttle.
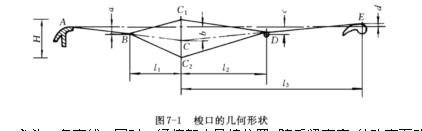
In the loom line, A, B, C must be a straight line. At the same time, through the guided rod position C then change the frame beam height d change, the CDF is always in a line. General thoracic beam height unchanged, chest beam surface is often used as a benchmark to measure the fabric export, the usual heald heald eye beam and beam height relative to the chest. The cloth and the usual eye position in general does not change once it is determined by the warp position line, in the actual production of the adjustment, specifically refers to the change of the beam height, front and rear position.
No.2 Shed formation
Different types of shedding mechanisms are not identical in forming openings in the shedding process. According to the movement characteristics of warp in the opening process, they are divided into central closed shed, fully opened shed and half shed.
(1) central closed shed;
In each opening movement, all the warp yarns are started from the heald position, and are separated from the upper and lower directions in two directions to form the desired shed. When the shed closes, all the upper and lower layers must be returned to the heald position. The opening way regardless of the heald frame under a warp opening is kept in the original position, must return to the IMIS position, then according to the requirements of the next shed by the heald level position, such as (1) is shown in figure 7-2. The weave of the figure is twill, and the weave of the fabric is shown in figure (4).
The opening way centreclosedshed, opening in the process of the changes of the lower warp tension, can be regulated by the concentration of the beam swing. Because every time warp can return to the IMIS position, so the processing is convenient in folding. But this way of opening increases the number of tension and friction of the warp and may increase the breakage of the warp. When the shed is formed, all the warp yarns are in motion, the shed is not stable enough, and the weft insertion is unfavorable. The dobby shedding mechanism or jacquard shedding mechanism of some wool looms and silk looms adopts an opening with a central closed shed.
(two) fully open shed;
This opening requires only the next opening, where the warp should be shifted up to a new position, while the rest of the warp is kept stationary, as shown in Figure 7-2 (2). The opening way open shed to reduce the number of warp tension in the process of opening and friction, to reduce the warp breakage rate, and the formation of the shed when only part of the warp shed in the movement is stable, is also beneficial for weft insertion. However, when the warp yarns are not assembled together, a flat heald device should be specially arranged for weaving the non plain weave fabric, so as to handle the warp broken ends. Three opening mechanisms, cam, dobby and jacquard, can be opened with full open shed.
(three) half shed;
The open and open shed is basically the same, in accordance with the fabric requirements, only part of the warp exchange position, and the need to stay on the lower of the warp to remain intact, but need to stay in the top of the warp will be slightly decreased, then the next time in the formation of the shed to rise to its original position, as shown in Fig. 7-2 (3) shows, some dobby used in this way.
Three, the clarity of the shed
Multi heald loom weaving is often used, considering the heald lifting movement does not interfere with each other, and a certain distance to each other, so the heald to cloth and the distance is not the same. The movement of each page makes the shed fully open and forms a shed with different clarity. The clarity of the shed has an important influence on the smooth weft insertion and the reduction of the warp breakage.
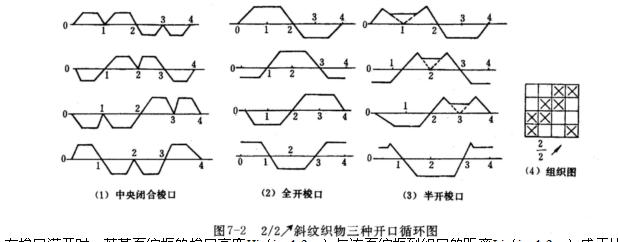
At the end of the shed, if the height of the web of a heald frame is Hi (i=1,2... ) the distance from the page frame to the weaving mouth is Li (i=1,2... ) is proportional to the shed in front of the top line should be in a plane, the lower warp in another plane, the shuttle called clear shed, such as (1) is shown in figure 7-3. Under the same conditions, the front shed is the most effective space, filling the best conditions, however, when the number of pages or more heald heald frame spacing is large, after a few pages of the heald frame shed height is too large, so that the corresponding warp elongation is too large, resulting in. In order to alleviate this contradiction, usually after a few pages of the heald frame shed height decreasing, the lower warp not in a plane, the upper warp is not in another plane, the shuttle is called a non clear shed, as shown in Figure 7-3 (2). Although the dynamic process of narrowing the gap between the shed the heald frame, the warp tension is relatively uniform, but the effective space is small, on the weft is extremely unfavorable, easy to cause the warp breakage, jump flower, shuttle and shuttle, weaving defects or faults, the shuttle is generally not used in the actual production, and the use of half clear shed, namely the lower warp is in the same plane, the upper warp not in one plane of the shed, as shown in Figure 7-3 (3). When weaving fine tex high density by plain fabric (such as feather cloth, poplin, etc.) usually adopts double shed, as shown in figure 7-4. The shed is not clear shed, no matter in the upper or lower delta, warp third harnesses the warp is always higher than that of the first page in the Delta, warp fourth page warp is higher than that of the second heald, thus shedleveling staggered the first three pages, four pages, second heald frame and heald frame. When all goes to the phase warp density in half, is conducive to the opening and cleaning shed.
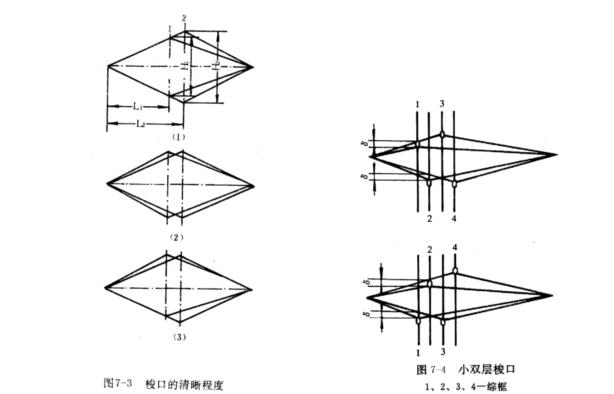
Four, tensile deformation of warp yarn
Effect of 1. shed height on tensile deformation
In the shed at the rear of a certain length under the condition of deformation and warp almost shed height is proportional to the square, in the fast deformation condition, the elongation of warp elongation deformation caused by the same force is proportional to the height of the shed will cause a small increase of warp tension increased significantly. Therefore, the height of the shed should be minimized as long as the filling is carried smoothly through the shed.
To determine the reasonable height of the shed, involving many factors, it is necessary to consider the structure and size of the weft insertion device, and also taking into account the reasonable matching of weft motion and movement of the sley, and the structure and properties of warp and fabric varieties of factors such as fabric. Usually, when the reed is in the final position, the reasonable height of the shed is determined according to the structure size of the weft insertion device. The shuttle loom as an example, according to the height and width of the shuttle, while paying attention to the last position when the pendulum effect is through the shuttle shed on the condition of 2 shed length on the tensile deformation of the sley
When the length of the back of the shed increases, the tensile deformation decreases; on the contrary, the tensile deformation increases. This factor is flexible in production, in actual processing, in yarn material, and in woven fabric. For example, because the strength of silk is small, the length of the back of the loom is usually enlarged. For example, when weaving high density fabric, the length of the back of the shed can be shortened, and the opening of the shed can be opened by increasing the tensile deformation and the tension of the warp.
3 back beam height and tensile deformation
Back beam height will affect the shed on the difference between the lower warp tension, which can be affected by the following three conditions to be investigated:
(1) in the beam line: at this time, delta lambda (Δλ) =0, upper and lower warp tension are equal,the formation of tension in the shed.
(2) in the line above the beam: at the delta lambda(Δλ) >0,the lower the yarn tension is greater than the upper warp tension, ranging from the shed form. The difference of the warp tension between the upper and lower layers will increase the back beam and the upper lift of the stop frame.
(3) in the rear line below: Delta lambda (Δλ) <0,lower warp tension is less than the upper warp,but this kind of unequal tension shed rarely used in actual production.
Second section opening motion law
In the process of opening, the warp yarn forms a shed from the action of the heald frame movement,and the nature of the heald motion has a great influence on the broken ends of the warp.After the shape and size of the shed are determined, the rule of heald motion becomes the fundamental factor affecting the opening movement.It is important to ensure the smooth weaving and improve the productivity and fabric quality of the loom.
I.angle and its distribution of heald frames
(1) indication of angle of heald motion
Each rotation of the loom spindle produces a spindle opening,and the time required is called an opening cycle.In an opening cycle,the motion of the warp passes through three periods:
In the 1. opening period, the warp is removed from the heald position and separated up and down until the shed is full;
2. at the end of the stationary period, when the shed is fully opened, the warp must be stationary for some time in order to allow the filling to have enough time to pass through the shed;
3. the warp in the closed period is stationary after a period of time and then returns to the heald position from the full opening of the shed.
The warp is separated from the heald position, up and down, to complete the opening once it is returned to this position. In the process of opening, the time that the upper and lower alternating yarns reach the heald position, i.e. the opening of the shed opening, is called the opening time, commonly known as the leveling time, and it is an important process parameter. Usually, the main axis of a loom marked with the kinematic time parameter of a loom is called a work circle graph of a loom, which is used to represent the coordination relation of the loom movement time, as shown in figure 7-6. The arrow in the picture indicates the direction of the spindle rotation. In addition to the individual case, the spindle always rotates in counter clockwise direction. The four characteristic positions of the front, bottom, rear and top of the circumferential chart (denoted as a, B, C, d) are called the anterior, lower, back, and upper heart, respectively. When the swing reed reaches the first and last positions, e and F, the positions of the main shaft are called the front dead center and the last stop point. The spindle position angle of the front dead center is 0 degrees, as the benchmark. The opening time in Fig. is indicated by an opening angle alpha K, and the rest time is represented by the stationary angle alpha J, and the length of the closed period is expressed by a closed angle alpha B. In the closing and opening times, the heald frame is in motion, so the alpha b+ alpha K is the heald motion angle. It should be pointed out that the coordination relation of the motion time of a loom's main mechanism is sometimes expressed in a periodogram.
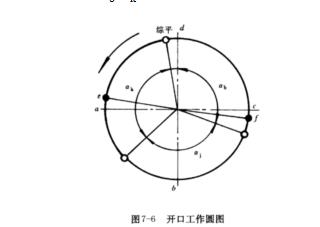
(II) the distribution of heald motion angles
The distribution of the opening angle, the stationary angle and the closing angle vary with the loom width, the fabric type, the weft insertion mode and the opening mechanism type. In a loom, the shuttle can smoothly pass through the shed for static heald frame angle is bigger, but the increase of the angle of repose, will narrow the opening angle and closed mouth, thus affecting the stability of heald frame motion. Therefore, the plain fabric, in order to take into account the motion of the shuttle and the heald frame motion, often make the opening angle, angle of repose and closed angle for each spindle, namely 120 degrees; with the increase of width in the loom, weft shed in flight time will also increase, therefore, should be appropriate to increase the static angle check the heald frame, and open mouth and closed angle is reduced; in the more than three pages of heald weave twill and satin fabric, in order to reduce the pressure angle of cam, improve the stress state, often the opening angle and closed mouth expanding; the connecting rod in an air jet loom shedding mechanism. The structure of this mechanism, the opening angle and the closed angle is larger, while the rest angle is zero; in the opening cam design of high-speed loom, considering in the opening process of load shedding mechanism is gradually increased, and in the process of closing the opening mechanism The load is gradually reduced, and the opening angle is larger than the closing angle in order to make the heald motion smooth and reduce the uneven wear of the cam.
Two, heald frame movement law
The rule of heald motion indicates the relation between the displacement of heald frame in motion (closed and opening) and the angle of rotation of spindle, t, and it has a great influence on warp breaking and loom vibration. The common rules of heald motion include simple harmonic motion and elliptical specific motion. With the increase of loom speed, the law of polynomial motion has been adopted more and more
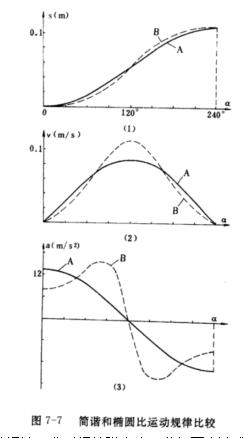
It can be seen that in the heald level before and after the heald frame motion quickly, the warp tension is small, does not result in breakage, but also conducive to the opening and cleaning shed; and a period in the closed after the start of the heald frame motion is slow, the shuttle flew out of the shed advantageous. But because the acceleration of the frame from static to motion and from motion to rest is not zero, the vibration of the heald frame is not conducive to high-speed movement. Therefore, the law of simple harmonic motion is generally used in the shedding mechanism of low speed looms (such as shuttle looms).
2. ellipse ratio motion law
When a fixed point rotates on an ellipse at the same speed as the center of the center, the motion of this point on the elliptical axis is the ratio of the ellipse to the motion. When the ratio of the length and the length of the ellipse to the ellipse is 1, that is the law of simple harmonic motion. The ratio of the ratio of the length of the ellipse to the axis of the ellipse has a great influence on the acceleration range of the frame motion. Generally, the ratio is from 1.2 to 1.3. If SX, Omega and alpha Y values with the ratio of 1.2008, and the maximum acceleration of heald frame harmonic motion is the same, but the frame from rest to exercise and from dynamic to static transition between the acceleration values than the simple harmonic motion of the small; when the ratio is greater than 1.2008, the heald frame acceleration maximum value exceeds the harmonic the heald frame motion, from static to moving and static value becomes smaller to transition between the acceleration from motion. Figure 7-7 curve in B are elliptic motion than displacement, velocity and acceleration curve, compared with simple harmonic motion, in the heald level before and after hours of warp tension, elliptical ratio movement of heald frame motion faster, more conducive to the opening and cleaning shed; in a closed period after the start of the heald frame motion more slowly, more conducive to the shuttle to fly out of the shed; frame from rest to exercise and from dynamic to static transition between the acceleration value is small, so small vibration heald frame.
3. polynomial motion law
There are many laws of polynomial motion in heald frames, one of which is displacement equation:
S=(SX/2)[35(ωt/αy)4-84(ωt/αy)5+70(ωt/αy)6-20(ωt/αy)7] (7-6)
The law of motion can make the instantaneous acceleration of the start of the heald frame and the end of the movement zero, thus avoiding the vibration of the heald frame and being suitable for the high-speed operation of the loom.
Relationship between process parameters and fabric formation in third looms
First, the relationship between warp tension and fabric formation
The warp tension on the warp means the static tension of the warp. When the tension is large, the warp tension at the mouth of the weft is greater, too little warp buckling and more buckling of the weft. In the process of weaving, the interaction between warp and weft is intensified, and the resistance of beating up is increased. On the other hand, if the tension of the machine is small, the warp tension at the ends of the yarn is smaller when the weft is beating. At the same time, the warp of the weft is less and the warp is buckling, and the interaction of warp and weft is weakened in the process of weaving. In the production, to choose the appropriate tension, if the warp tension is too large, because the strength of warp breakage will increase; if not, the warp tension is too small, the beating fell displacenment volume, accentuated by the warp and the eye will also increase the friction, breakage.
The magnitude of the tension on the machine has a great influence on the width of the beating area during weaving. From the above analysis the composition of the basic reason of beating area width changes, beating area width will change with different tension caused by the fabric stiffness and tension, such as weaving 14.5tex * 14.5tex yarn poplin in loom, with the increase of tension K, beating area width decreased, such as Fig. 9-11 showed regular changes with negative exponential curve. You can see from the figure, from the reduction of the warp breakage rate in weaving process to consider adopting appropriate large tension in weaving the yarn poplin timely, and this high density fabric tension should be bigger in order to meet the opening and cleaning shed and tighten the weft is consistent with the requirements of the. But when weaving other fabrics, the tension should be determined according to the specific conditions.
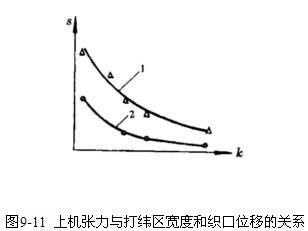
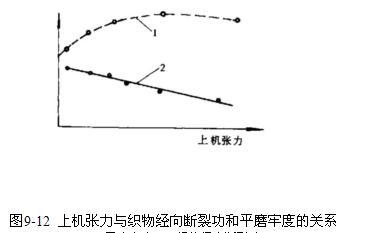
Figure 9- machine tension and beating width and fabric displacement, in order to improve the smoothness of fabric, it is better to adopt larger mechanical tension. For example, when most cotton fabrics are woven, if the tension is small, the surface of the fabric is not smooth enough and has a rough feel. When machining the fabric warp tension unevenness on the shaft, it may be appropriate to increase the tension, so that the fabric is relatively smooth, but also can reduce the tension difference between yarn and yarn, so as to compensate the unevenness of yarn tension in a certain extent, the shadow reduction, fabric leveling. Another example is in the spinning of light spinning, if the use of smaller tension on the machine, the formation of the silk surface is not smooth, and produce an elastic edge, when the machine tension increased properly, the quality of the silk surface greatly improved, smooth and shiny.
But from the fabric mechanical properties, should not be used on larger tension, when the tension increases, fabric thickness, weight, strength and warp density changes little, but was reduced to shrinkage and elongation is larger. The research shows that the fastness of the fabric is related to the warp fracture work and the size of the weft surface of the warp and weft yarn on the fabric surface. When the warp fracture work and support surface are large, the fastness is also large. With lesser tension, fabric warp breaking work at the same time greatly; tension with proper small, Qu Qu Bo yarn high is close to 1, the weft yarn also exposed on the surface of the fabric, increase support, to overcome the tension of large weft buckling in more warp the surface of the fabric revealed less, thus support the disadvantage of smaller. Figure 9-12 is a plain weave 29tex * 29tex in the fabric after changes to the work of fracture peace with different tension of grinding fastness. It can be seen from the diagram that if the machine tension is medium and small, then the fabric will have a greater fastness to fracture work and abrasion.
Figure 9-12 tension and fabric to fracture work of peace fastness must also pointed out that the larger the tension, the fabric shrinkage is large, the direct for clothing, fabric, this will give them the losses.
What kind of machine tension should be used depends on the specific situation. For example, the total number of warp yarn in weaving closely woven fabric, in order to open the shed and made clear the weft yarn, it may be appropriate to increase the tension; when weaving thin fabric or artificial cotton fabric, warp tension should be properly reduced, in order to reduce the warp breakage rate. Such as weaving twill fabrics, taking into account the need to have a unique style of a diagonal line convex degree, should not be used on the tension of the. The plain fabric, under the same conditions, for the matter should be used in weft, loom tension larger.
Two, back beam height and fabric forming relationship
Has been introduced in the opening chapter, a beating when the shed is between the lower layer warp tension difference determines the back beam height, the difference of beating process and fabric formation has great influence.
In weaving, the average density of the warp in the fabric is essentially determined by the reeds. The reed tooth thickness, when the number of warp eachreed penetrate the teeth in 2 roots and 2 root above, between the warp distance is not the same, between the warp between reed and the smaller distance between adjacent warp dent on both sides of the distance is larger. When weaving warp density is not very high plain weave fabrics, warp in the width direction (i.e. horizontal) uneven arrangement of this law, and in the process as the weft threads are not changed, then the fabric will appear in Reed Road defect. Of course, this kind of fabric appears to be eliminated by fabric finishing.
In weaving, the use of warp tension between the upper and lower layers can also prevent the appearance of the reed path on the cloth. Because the adjacent range tension of shed warp in a relatively tight, a relatively loose, intertwined, due to tight buckling force as many layers of warp weft, weft and warp on layer have a greater pressure, under pressure, make the loose layer warp get larger lateral movement, to eliminate the disadvantages of uneven arrangement the warp, Reed Road to avoid defects, achieve plumpy hand requirements.
The lower the warp tension tension ranging from shuttle a bigger opening with less than 90 degrees angle (the angle between the beating reed mouth and fabric cloth), to quickly reduce weft weft, reed back backwash, forming close thick fabric.
Plain weave fabric, generally use the high beam height, can obtain the full fabric appearance. But in the cotton processing warp is low, large number of warp density such as 14.5tex * 14.5tex yarn poplin, as the warp density, so the beam height can be slightly lower, not due to the warp tension caused by too small opening is not clear, cause jump flower weaving defects, also not due to the lower the yarn tension large and cause a lot of broken ends. The same reason, in weaving chemical fiber blended fabrics, chemical fiber yarn is easy to cause the opening due to pilling is not clear, so the beam height can be lower than cotton.
In fact, in woven twill fabrics, often with low beam process, the upper and lower warp tension is nearly equal, which is mainly based on the appearance quality of fabric unique to decide. This unique quality of the appearance of the twill lines on the surface of the fabric has a deep, uniform, straight, clear effect. In the loom, in order to obtain the clear effect, should avoid too large tension, to ensure the depth of lines, to bump clear, still need to use the upper and lower warp tension is nearly equal to obtain uniform straight stripes. This is especially important for double faced twill. But in the woven twill cloth, in order to make positive lines with a larger depth of twill, can make the back rest a little than woven double-sided twill when high. At the same time, in the double-sided twill for tightness high, is conducive to tighten the weft side, also often makes the height of some.
In weave and satin fabric, the beam configuration in the upper and lower warp tension nearly equal position, so that the warp breakage rate is reduced, pattern even, comprehensive mechanism work next time is easy. But in a close weave satin fabric, its also slightly improved.
Three, relation between opening time and fabric formation
The opening time (leveling time) is early or late, which determines the size of the height of the shed when beating, and the size of the height of the shed determines the magnitude of the warp tension at the instant of the beating. The opening time is early, and the warp tension at the ends of the yarn is big while the other is small. In the high beam work, beating when shed height size, but also determines the difference between the lower warp tension when beating up on. Therefore, in a certain range of early opening time and beating up, the tension difference between the upper and lower layers at the upper and lower levels of the fabric will be larger; otherwise, it will be smaller.
Therefore, the relationship between the opening time and the formation of fabrics, basically with the front tension and back beam height and the relationship between the formation of the same fabric.
But it should be pointed out that opening time has a unique influence on the weaving process. Because of the different height of the shed at the time of beating, the inclination of the warp between the upper and lower layers of the fabric is different. Therefore, although the swing of the reed does not change, the friction length of the warp layer is different. The opening time is early, the greater the length of friction, and the tension is larger, it is easy to make the yarn structure destroyed and broken, so with the opening time sooner or later, will have a different warp breakage rate changes. At the same time, due to the shed opening degree is different, as previously shown in Figure 9-8, beating two cross layer warp angle is different, so the change of the warp and weft angle surrounded the weft beating up resistance and reed back backwash volume will change. The opening time is earlier, the beating resistance is large, the volume of the weft is small, and it is easy to knit into a compact and thick product. On the contrary, the opposite is true. In addition, the opening time of the early late, but also affects the yarn in the warp shed by warp clipped early late, and shed the warp of import shuttle shuttle extrusion, the former is related to whether there is shrinkage, which is related to whether there is fault lines and rolling spindle. Therefore, when the opening time is determined, both the weft insertion time and the weft insertion time should be taken into account.
In actual production, when weaving plain woven fabric, according to the requirements of different varieties, different opening time is adopted, and the early opening time is usually adopted. In weave twill and satin fabric, warp density encountered, it must use the opening time, to reduce the length of warp tension and friction, to prevent too much warp breakage. In addition from the lines clear and neat pattern consideration, usually in the woven twill and satin fabric, should adopt the late opening.
In order to prevent the reed from rubbing excessively against the warp when weaving the larger weft fabric, the late opening time should be adopted without affecting the solid beating condition.
The fourth section of fabric barres
A defect fabric refers to the surface of the fabric for loom performance, improper operation caused by uneven weft arrangement defects in high density and low density reflect more fabric. With the weaving technology and electrical integration of the continuous improvement of the degree of fabric barres has greatly reduced. Barres is a kind of serious fabric defects, and has a great influence on the physical quality of fabric.
First, the relation between loom beating up and fabric formation
In the process of beating, the weft yarn overcomes the frictional resistance between the warp and weft yarns under the action of the reed, and F1 moves along the warp yarn toward the front of the machine. When the weft reaches the front dead center, the difference between the warp tension and the fabric tension F is relative to the magnitude of the friction resistance F1, which determines whether the relative movement of the weft yarn is relative to the warp slip or the movement of the yarn with the warp. The former occurs in Delta F﹥F1, which causes weft density of fabric to grow, and the latter takes place at Delta F﹤f1, which does not contribute to the increase of fabric weft density.
In normal rotation of the loom, the relative slippage of the weft yarn and the amount of movement of the weft yarn in the fabric formation are proportional to the weft density of the fabric. As soon as the loom running condition changes, the relative slip and co movement ratio may change, causing a change in fabric weft density accordingly.
At the beginning of each beating motion, both the front and back of the fabric position have a great influence on the fabric formation. Loom during normal operation, the fabric in a certain position, can be woven into the fabric of qualified Weimi. For some reason, the position of the weaving position shifts to the back of the machine, and the impact of the reed on the opening of the fabric will be strengthened, and the slippage of the weft relative to the warp will increase, so that the weft density of the fabric will increase; otherwise, the weft density will decrease.
Therefore, when the warp tension and the position of the mouth are changed relative to the normal operation of the loom, it is possible to change the weft density of the fabric (as opposed to the unevenness of the weft arrangement in other fabric areas). When the change to a certain extent, may be instruments or eye detection, to determine the fabric barres.
The types and causes of fabric defects. Many, mainly has the following several kinds. Around to reduce and prevent the fabric barres modern shuttleless weaving machine technology, made a series of improvements.
Two, the switch caused by defect rail car loom
When the loom switches the car, the speed of the loom is obviously lower than the normal speed, which caused it
The 1 opening process and warp deformation rate of warp stiffness decreased, while the deformation speed is reduced when the warp opening did not change, but the warp stiffness decreased, so the reed beating to stop before the warp tension near the lower, then F was reduced, and the warp weft move together to increase the amount of relative slip reduction the weft density decreased, may cause the switch car barres, barres.
2. in the inertial beating weft looms (such as shuttle looms), the inertial force of the reed beating motion is proportional to the square of the loom speed. When the loom is in normal operation, the beating force is mainly supplied by the inertia force of the reed block. The decrease of the loom speed leads to the decrease of the inertia beating force, and the beating force is mainly obtained from the motor through the main shaft, the crank and the hand. Since there is a gap between the hand and the hand bolts, two different speeds make the gap e position and the reed reach the forward position, as shown in Figure 12-1 (a) (B). Obviously, in the two case, the reed reaches the most forward position, producing a certain distance difference. When the gap is larger, the distance difference is obvious, the formation of aligned weft in the fabric is not uniform, the switch car barres.
3. a large number of studies have pointed out that the friction factor between the warp and weft yarns is related to the slip speed between them. Because fiber and yarn structure are different, there is a positive or negative correlation between them. The change of friction coefficient of warp and weft yarns leads to the change of relative slippage and joint movement of weft yarn, which results in change of weft density. Therefore, the loom switch car may cause yarn friction factors change through the loom speed decreased, resulting in the weft density change, produce fabric barres serious.
Shuttleless loom weaving shaft to roll back a certain amount of warp drive, the warp tension increment rewind is generated by the compensation of delta F decreases the number, the F compensation to the normal number, to avoid the formation of fabric defects of starting marks. Part of the shuttleless loom with recoil back, loom driving beam recoil, in order to improve the warp tension, play the role of compensation F.
To overcome the switch car barres positive method is the use of ultra starting torque motor, the starting torque of the motor is 12 times of the rated torque, starting after the first turn in that loom speed achieved the normal speed of 80%~90%, fundamentally avoid weft warp stiffness and the yarn tension decreased.
Loom weft in the inertia, reduced body clearance (there is a gap between the loom and hand in hand bolt E) or a non inertial beating, have certain effect to reduce the switch car barres.
Three, loom by rail defect caused by bad
The bad result of warp feeding is the uneven tension of the warp yarn. When the weft is beating, the warp tension is too large. When beating, the relative slippage of the weft yarn is much, but the amount of the movement is less and the weft density of the fabric is high. On the contrary, the amount of movement is more and the relative slippage is less, and the weft density of fabric is low. With the progress of warp weaving technology, the warp feeding mechanism is developed from simple mechanical delivery to mechanical stepless regulation, let off and close switch type electronic let off until the advanced sensor electronic let off. The warp caused by the fabric barres has been greatly reduced.
Sensor type ELO can meet the warp tension micro regulatory requirements, due to the complicated mechanical adjustment mechanism to get rid of the whole, regulating inertia decreases, adopt the warp tension sensor at the same time, the small change of warp tension rapid detection and timely feedback, so that the warp tension fluctuation could be suppressed rapidly, ensure warp the previous constant tension beating, prevent the defects caused by the warp rung.
Four, loom defects caused by the bad.
The holding force of a loom winding mechanism influences whether the position of the fabric can be stably controlled. Especially the fabric organ after the car, due to poor take-up mechanism of fabric grip, the cloth will move slowly to the machine direction, causing a fabric defect of weft next time when driving, especially when the high tension of warp knitting.
Therefore, the take-up mechanism of the loom has been improved accordingly, such as increasing the diameter of the roll of the rough surface, selecting the best coating material, increasing the pressure of the compression roller and changing the compression mode, etc.. The full width of the edge supports the fabric very well and is used in weaving non coated high density airbag fabrics.
Five, the warp yarn and fabric caused by creep barres
When weaving looms for a long time, warp and fabric are still stretched under certain tension and creep occurs. As a result of creep, the position of the weaving mouth moves forward or backward relative to the normal position. Although the weaving method requires the operator to loosen the warp when the loom stops for a long time, the warp tension still exists, and creep is unavoidable. When the loom drive, if weaving position and the warp tension is not accurate, then the fabric defect rungs will produce uneven weft density.
The creep properties of yarn and fabric are different, but the common point is that their deformation amount increases exponentially with the time delay, and their growth rate decreases rapidly. This factor is taken into account when the new shuttleless loom is used to adjust the position of the loom and the warp tension. The amount of adjustment varies with the parking time.
A defect caused by creep occurred in the process of yarn loom switch in the car, so it can be placed in the car barres loom switch.
The above article originates from China Textile Machinery Network