Loom Maintenance-Adjustment And Influence Of Warp Tension Of Different Fabrics
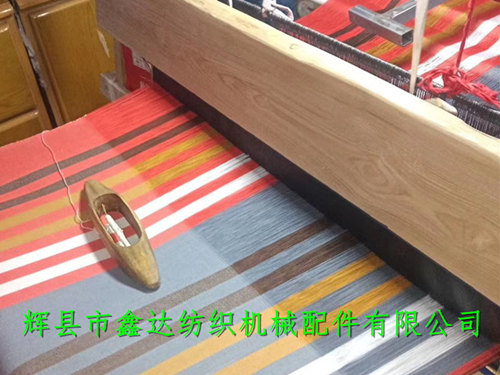
The basic knowledge of loom maintenance-the adjustment and influence of warp tension of different fabrics, the positioning of warp position line and the adjustment of loom tension are all carried out around the height of loom back beam, the position of heald frame and the size of shed. The maintenance of plain loom, the adjustment of twill loom cloth width and the relationship between lower warp yarn and breast beam also affect the theoretical judgment and efficiency improvement in loom maintenance.
One,Meridional position line
At the time of heddle, the warp yarn starts from the surface of the rear beam C28, passes through the top of the drop guide rod O39, passes through the heald eye, and reaches the weaving shed. This position of the warp yarn is called the warp position line.
With different warp position lines and shedding, the tension difference of the lower warp on the shed is different. Weaving different fabrics has different warp strength, warp density, beating-up resistance and fabric style, so it is required to prepare different warp tension differences between the upper and lower layers, that is, to prepare different warp position lines to meet their different weaving requirements.
Adjust different warp position lines, mainly to adjust the height of back beam and warp stop frame.
When weaving plain fabrics, the back beam is generally adjusted higher. If the back beam is too low, for example, when the warp position line connecting the back beam, the heald and the shed is in a straight line, the warp tension of the lower layer on the shed is basically equal. At this time, because the peak of warp tension caused by opening is very small, it is beneficial to reduce warp breakage; However, when beating-up, the warp yarn at the weaving shed is constrained by the separation of reeds, and reed marks (that is, square eye defects) are easy to appear on the cloth surface.
With the gradual improvement of the rear beam C28, the difference of warp tension between the upper and lower layers gradually expands. When the back beam is raised to a certain extent, for example, the back bar brackets C1 and C2 are raised to 70mm away from the upper plane of the wall panels P1 and P2, that is, the surface of the back beam is 22mm higher than the surface of the breast beam P3, the warp tension difference between the upper and lower layers will be quite large. At this time, the relevant dimensions of the warp position line are shown in Figure 1-1.
Under this condition, when the weft is pushed by the reed to the forming zone, the weft will inevitably slide relatively along the layer with high tension, and drive the layer with low tension to move in the same direction, which makes the layer with low tension appear slack segments between the weft yarns in the fabric forming zone one step ahead of the reed. The reed pressed these loose segments to bend forward, so the warp did not "separate and traverse" during most of the movement of the reed. In addition, because the tension of the upper and lower warp yarns changes with each rotation of the crank, this provides an important decisive condition for the "even gap traverse" of the warp yarns in the fabric forming area. Therefore, proper tension difference between the upper and lower warp yarns will help to arrange the warp yarns evenly in the fabric, eliminate the reed marks (square eyes) and improve the fullness of the fabric.
However, if the back beam is raised too much, the tension of the lower warp will be too great, which will increase the warp breakage; The tension of the upper warp is too small, which makes the shed unclear, increases weaving defects and makes the cloth surface rough.
When the twill fabric is beating-up, some warp yarns are full and motionless, and some warp yarns are moving up and down, so there is already a tension difference between the warp yarns of each layer. In order to reduce warp breakage and weaving defects, the back beam should be lowered appropriately, but it is too low to make the cloth uneven.
Whether weaving plain or twill fabrics, the height of guide rod O39 in warp stop depends on the position of rear beam C28. General requirements: At the time of heddle, the warp yarns from the rear heddle eye to the surface of the rear beam C28 are in a straight line, and the upper surface of the drop guide rod O39 is just next to the warp yarns, so that the warp yarns are neither empty nor lifted. If it is empty, it will make the drop wire jump violently when beating; If the warp is lifted, the middle guide rod O39 will grind out of the groove and increase the extra resistance of the warp.
Second,Upper tension
The tension on the loom generally refers to the static tension on the warp yarn during the heddle. Adjusting the tension of the upper machine mainly depends on moving the position of the tension weight C17 on the tension weight rod C14. Under special circumstances, the number of weights can be increased on the tension weight rod C14, or the up-and-down position of the let-off hanger C33 can be adjusted.
The tension on the machine affects the appearance, quality and width of the fabric.
(1)Influence on fabric appearance
When beating-up, the reed pushes the weft yarn to move along the warp yarn to the shed. When the tension of the warp yarn behind the weft yarn is greater than the sum of the tension of the warp yarn in front of it and the friction resistance of the weft yarn moving forward (that is, beating-up resistance), the weft yarn can slide relatively along the warp yarn. Otherwise, when the warp tension difference between the front and rear parts is not enough to overcome the beating-up resistance, the weft can only drag the warp and drive in the same direction. Until the tension difference between the front and back warp yarns is enough to overcome the beating-up resistance, the weft yarns can slide relatively. In each beating-up process, this kind of relative sliding co-directional driving appears alternately. The beating-up resistance of different fabrics is different, so the corresponding tension is required to make the weaving process normal. For example, when the tension on the loom is too small, the warp yarns must be driven in the same direction when beating up, so that the weft yarns can be fastened. Therefore, the warp yarns dragged back and forth in the heald eye will be rubbed, which will cause more broken ends, and the tension of the warp yarns in front of the reed is uneven, and the cloth surface appears uneven. When the tension on the loom is too high, because the warp yarns are driven less in the same direction, the forming area is small and the warp buckling wave is low, the cloth surface is not full and the grain is not clear.
(2)Influence on fabric defects
1.The tension on the machine is too small and the opening is unclear, which is easy to cause "three jumps" and shuttle failure.
2.Excessive tension on the loom is not conducive to the arrangement of warp yarns during beating-up, and obvious reed marks will remain on the fabric surface, forming square eye defects. Excessive tension will also increase warp breakage and cause shuttle rolling failure.
(3)Influence on width
The warp buckling wave of the fabric is low because of the high tension on the loom, and the fabric surface becomes narrow and long because of the elongation of the warp after tension. When the tension on the machine is small, the cloth is wide and short. However, the tension on the loom is large, and the retraction amount of the cloth roller is also large in the finishing process after falling, which is a matter to be paid attention to when controlling the cloth width on the loom. But the overall result is still that the greater the tension on the machine, the narrower the cloth width and the longer the cloth.
Reasonable adjustment of loom tension depends on the beating-up resistance when weaving various fabrics. The beating-up resistance of thick and dense fabrics is large, and the tension on the machine should be large; The beating-up resistance of thin fabric is small, and the tension on the machine should be small. In addition, yarn quality, beam quality, fabric appearance requirements, etc., are also important basis for determining the tension on the machine. The quality of the beam is good, and the tension and arrangement of the warp yarns are uniform, so that the tension on the loom can be smaller, so that the cloth surface is both uniform and full; The quality of the beam is poor, and the tension and arrangement of the warp yarns are uneven, so the tension on the loom should be larger to ensure the smoothness of the cloth surface first.